Why choose continuous screen changer for plastic granulation
Plastic granulation is divided into modified granulation and recycling granulation. For modified granulation, we can provide a variety of screen changer types and technical options, and strive to provide customers with filtration solutions, which are convenient for the cleaning and replacement of screws and barrels. In this way, the quality and craftsmanship of plastic products can be better realized. The granulation process is to dry the finely ground powder and add an adhesive to make particles with good fluidity and a particle size of about 0.1mm. Granulation is widely used in all aspects of production and life, and has a wide range of uses. In the production process of granulation, impurities in the melt need to be filtered out. The ordinary manual screen changer needs to change the screen frequently in the production process, which consumes a lot of manpower and material resources. In order to solve this situation, the continuous extrusion screen changer developed by Zhengzhou Batte pelletizer screen changer manufacturer can solve the above problems very well.
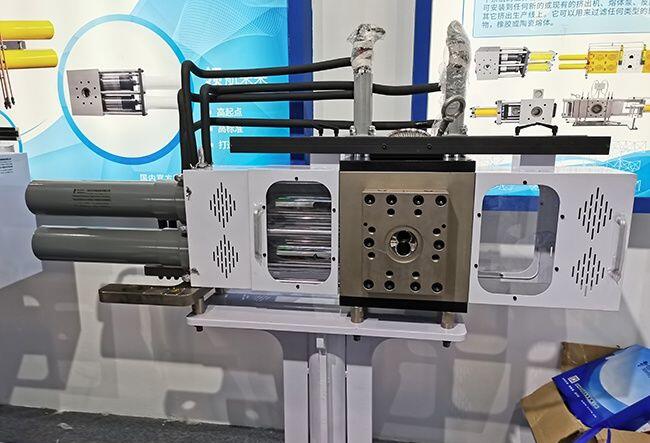
Non-stop continuous screen changer for plastic granulation is used for chemical fiber, blown film, flat film, cast film production, pipe, sheet, wire, fiber manufacturing, pelletizing line, recycling, etc. It can meet the production of high temperature, high pressure and high extrusion of any polymer material. It can be used in conjunction with extruders of different standards. It does not stop to change the screen, the product is not interrupted, and the material is not leaked.
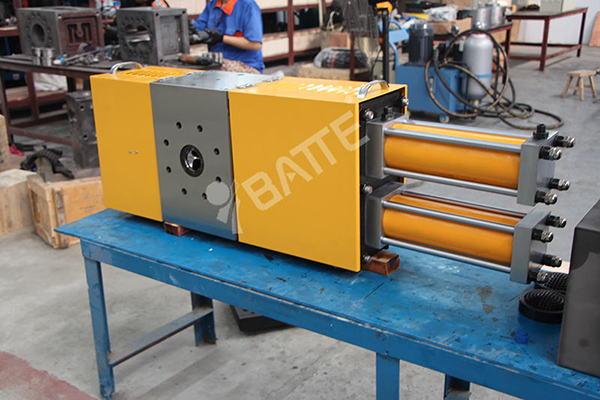
Features of hydraulic extrusion continuous screen changer for granulation:
1. There is no need to cool down or heat up, which reduces the loss of electric energy;
2. No shutdown or dismantling, which improves the production capacity and the work efficiency of workers, and increases the efficiency of the enterprise;
3. By filtering the impurities in the melt, the wear and tear of the impurities on the abrasive tool is reduced, and the service life of the abrasive tool is prolonged;
4. The important thing is to improve the quality of the product by filtering the impurities in the melt, which is directly reflected in the appearance of the smoothness;
5. No need to stop, dismantle the extruder flange to clean the impurities in front of the multi-plate holes (splitting plate), which reduces the labor intensity of workers, improves the production efficiency, and reduces the production of waste;
6. The use of continuous hydraulic extrusion screen changer is equivalent to increasing the length of the flow channel, improving the plasticization and homogeneity of the melt, and at the same time improving the quality of the product.
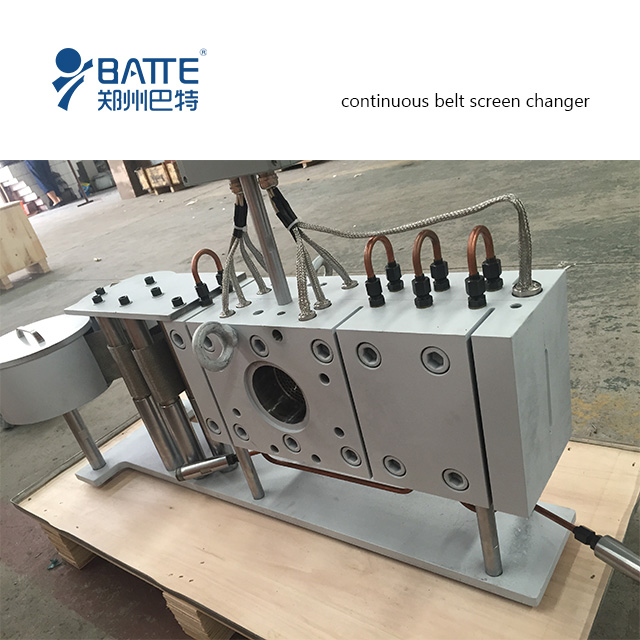
The production of the new material adopts a hydraulic screen changer, which can increase the plasticization and homogeneity of the melt, and is also a necessary guarantee for the granulation process. Although there is almost no impurities in the new material, in actual production, the impurities in the environment, Factors such as impurities generated during transportation and work also exist, so installing a screen changer is also a necessary quality assurance. The use of recycled materials and leftovers must use a non-stop screen changer to expand production capacity, reduce costs, improve efficiency and increase benefits. Zhengzhou Batte is a professional pelletizer screen changer manufacturer. The types of screen changers provided are divided into: plate screen changer, column screen changer, mesh belt screen changer, etc.